For any business person, nothing is worse than a malfunctioning ice machine. Whether you operate your business in food service or hospitality, the moment your ice machine suddenly breaks down, everything almost halts to a stop. Commercial ice machine repair goes beyond merely repairing a broken part to guarantee business continuity. If your ice machine is making strange noises, producing low or discoloured ice, or showing other weird signs, it might be time to call in the pros. Let us walk you through the warning signs that your commercial ice machine needs professional attention and explain why maintaining your commercial ice machine is essential to avoid costly repairs down the road.
Is Your Ice Machine Acting Up?
Before you panic, let’s go through a few of the most common signs that it is time to call in a professional. If any of these red flags seem to be part of what your ice machine is exhibiting, know that it is not just a glitch; it’s a problem.
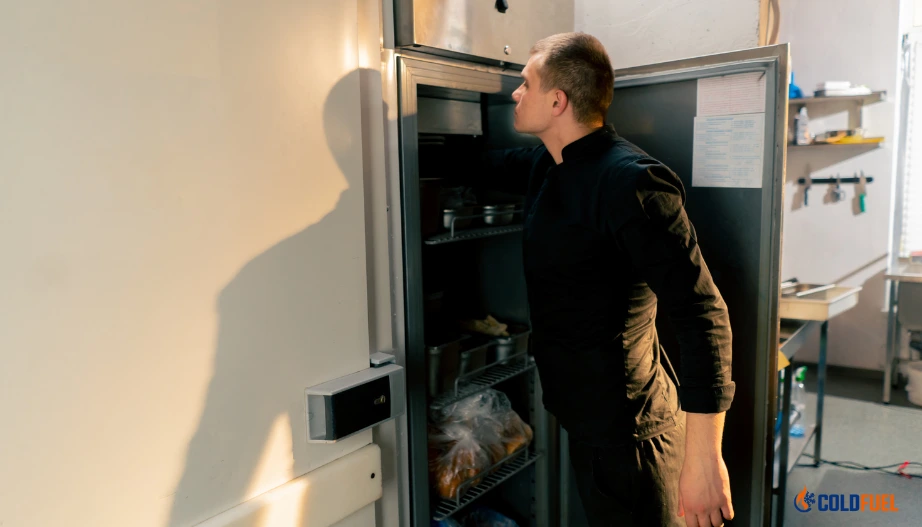
Strange Noises
Strange noises coming from your ice machine are typically one of the first signs that something isn’t as it should be. If your ice machine suddenly begins to make loud banging, grinding, or gurgling sounds, you can be sure a mechanical problem lurks inside. Most of the time, such noises signify issues with either the condenser, evaporator fan or compressor. Ignoring strange sounds will result in bigger problems down the line, so it is best to call in a professional to handle the commercial ice machine repair sooner rather than later.
Low Ice Production
When your ice machine isn’t cranking out ice at the rate it used to, that’s a major red flag. Clogged water filters, a failing water pump, or low refrigerant levels could cause low ice production. If your ice machine isn’t meeting demand, it can result in delays, unhappy customers, and a serious hit to your business. A technician can locate the root cause and restore full ice production in no time.
Discoloured or Cloudy Ice
Discoloured or cloudy ice isn’t just aesthetically unpleasant; it may even pose a health hazard. If your ice appears differently than usual, it may be a strange pink, cloudy, or another weird colour, which may signal contamination due to mineral buildup, mold, or bacteria. The water filtration system or water supply may be the problem, and professional commercial ice machine maintenance can resolve this quickly. You don’t want to take a chance with the health of your customers, so you will want to have any discoloration of the ice checked by an expert.
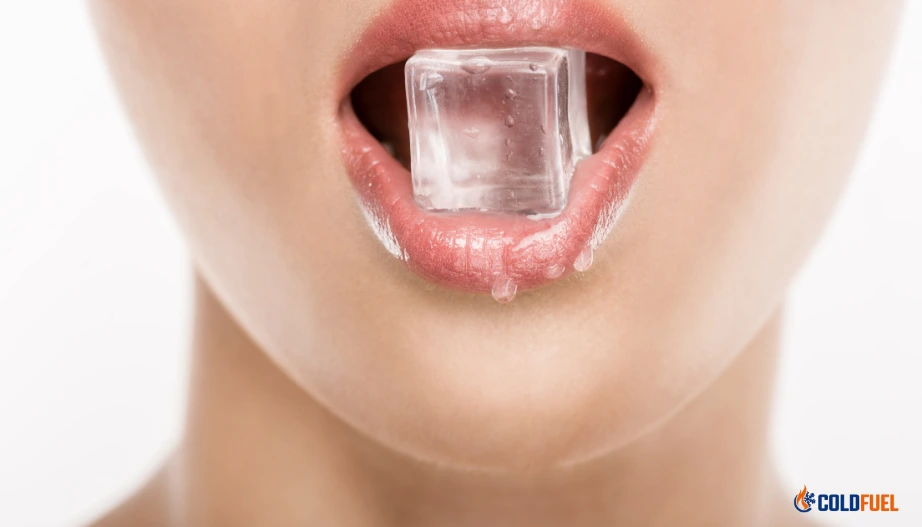
Other Signs You Shouldn’t Ignore
These other issues indicate further problems with your ice machine, so you shouldn’t ignore them for long.
Water Leaks
A leaking ice machine wastes water and can damage your machine or even the equipment around it. This is often due to disconnected hoses, blocked drainage, or problematic pumps. When you see water pooling at your machine or somewhere else, have a professional technician inspect the system and repair the leak before more damage occurs.
Bad-Tasting Ice
Ice is supposed to taste clean and fresh. If your ice tastes off or smells bad, that might indicate that something is wrong with the filtration system. Filthy water filters, mold, or bacteria can alter the taste of the ice and cause health risks to your consumers. This could be prevented if routine commercial ice machine maintenance were carried out. However, if it tastes bad, your ice calls for a professional to clean and sanitize your machine immediately.
Preventive Commercial Ice Machine Maintenance
Nobody’s happy when there is a broken ice machine, and the issues mentioned above can be countered with regular maintenance of commercial ice machines. Prevention is better than cure for your ice machine. Here are some things you can do:
- Clean Your Machine Regularly: Routine cleanings can prevent minerals and bacteria growth that can damage your system.
- Replace The Water Filters On Time: Change your water filters with time to maintain clean ice and to keep your machine running effectively.
- Schedule Regular Inspections: A technician will find minor problems that could become major ones. Preventive maintenance keeps everything running smoothly.
- Check The Refrigerant Levels: Low refrigerant can seriously impact ice production. Have your technician check these levels during routine inspections.
- Check The Condenser and Evaporator Coils: Periodic cleaning of the condenser and evaporator helps prevent cooling problems and keeps your machine running correctly.
Regular maintenance prevents breakdowns, saving time and money. Like tuning up your automobile, prevention is always less costly than repair.
When to Call in the Professionals
Don’t let little problems become huge headaches. If your ice machine is displaying any of the symptoms we discussed, such as strange noises, low ice production, or discolored ice, it is time to get in touch with the professionals. Here at Cold Fuel, we specialize in commercial ice machine repair and are ready to get your machine up and running. Our licensed technicians offer dependable service throughout Toronto and the GTA to keep your ice machine running smoothly and your business running on schedule.
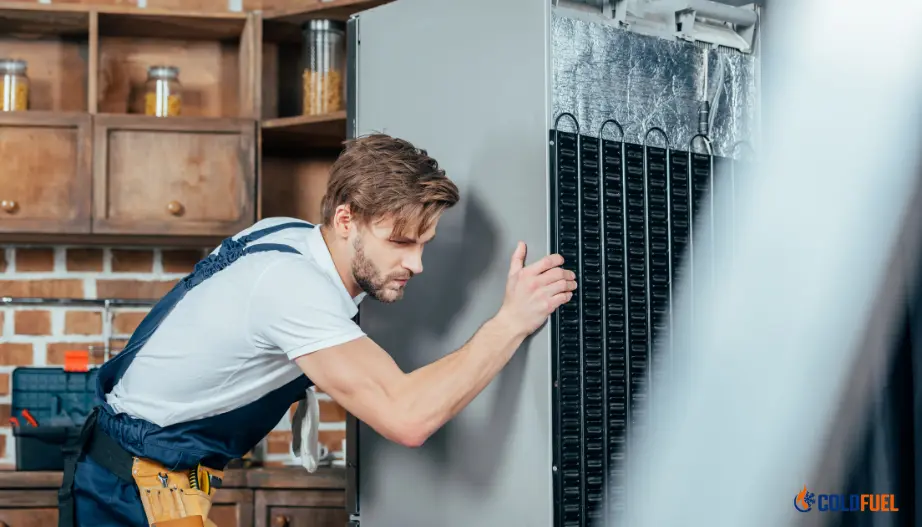
Avoid Problems With Professional Commercial Ice Machine Repair and Maintenance
Ignoring the problem will only make things worse. That’s why staying on top of commercial ice machine maintenance is crucial for your business. If your machine is showing any signs of trouble, don’t wait until it breaks down completely. Call in a professional technician to handle the problem quickly and efficiently.
At Cold Fuel, we offer full commercial ice machine repair services to keep your equipment running smoothly. A malfunctioning ice machine should not affect your business. Contact us today for a consultation or to schedule your repair! We’ve got you covered.